World Day for Safety and Health at Work 2023: A talk with Regina Kabwogi, HSE Lead
As we celebrate World Day for Safety and Health at Work, it is important to recognize the critical role that health, safety, and environmental (HSE) professionals play in protecting workers and safeguarding organizations. In industries such as energy, which involve complex and hazardous processes, HSE leaders are tasked with ensuring that every employee goes home safe and healthy every day.
To shed light on the challenges and best practices of HSE management in the energy sector, we had the opportunity to speak with Regina Kabwogi, one of our HSE Lead at CSI Energy Group. She has been instrumental in developing and implementing HSE policies, procedures, and programs that not only comply with regulatory requirements but also promote a culture of safety and continuous improvement.
1. How does CSI Energy Group prioritize Health and Safety, and why is it important to do so?
We believe that a safe working environment is not only a legal and ethical obligation but also a fundamental aspect of our business operations. We prioritize Health and Safety through a comprehensive approach that includes the development and implementation of policies, procedures, and training programs. We do have daily toolbox talks, conduct intensive induction to visitors and measure the performance of all our initiatives. We ensure that it (health & safety) is integrated into every aspect of our business operations, from project planning to execution, and from routine activities to emergency response.
We strive to create a safety culture within the Group, creating a set of shared values, beliefs, and attitudes that shape the way our people approach Health and Safety in the workplace. When a safety culture is established, it becomes ingrained in the organization's DNA, and it drives decision-making, behaviors, and attitudes across all levels of the organization.
The impact of a safety culture on business operations can be significant. When employees understand the importance of Health and Safety and how it relates to the success of the organization, they are more likely to prioritize it in their work. They are more likely to report near-misses, hazards, and unsafe conditions, which can be addressed before they become major safety incidents. This, in turn, reduces the frequency and severity of accidents and injuries, which can have a significant impact on productivity and the bottom line.
Additionally, creating a safety culture can improve employee engagement and morale. When employees feel safe and valued, they are more likely to be engaged in their work, which can lead to increased productivity and reduced turnover. It also creates a positive work environment, which can attract top talent and enhance the company's reputation as a responsible and sustainable employer.
From an employee perspective, a safety culture is critical for ensuring that they can return home safely to their families after each workday. It promotes a sense of ownership and responsibility for their own safety and the safety of their colleagues, which can lead to a sense of pride and satisfaction in their work.
Overall, creating a safety culture is not just about compliance with regulations or meeting targets; it is about creating a workplace where employees can thrive, and the organization can achieve long-term success. It requires a commitment from all levels of the organization, from top leadership to front-line employees, to prioritize Health and Safety in everything they do.
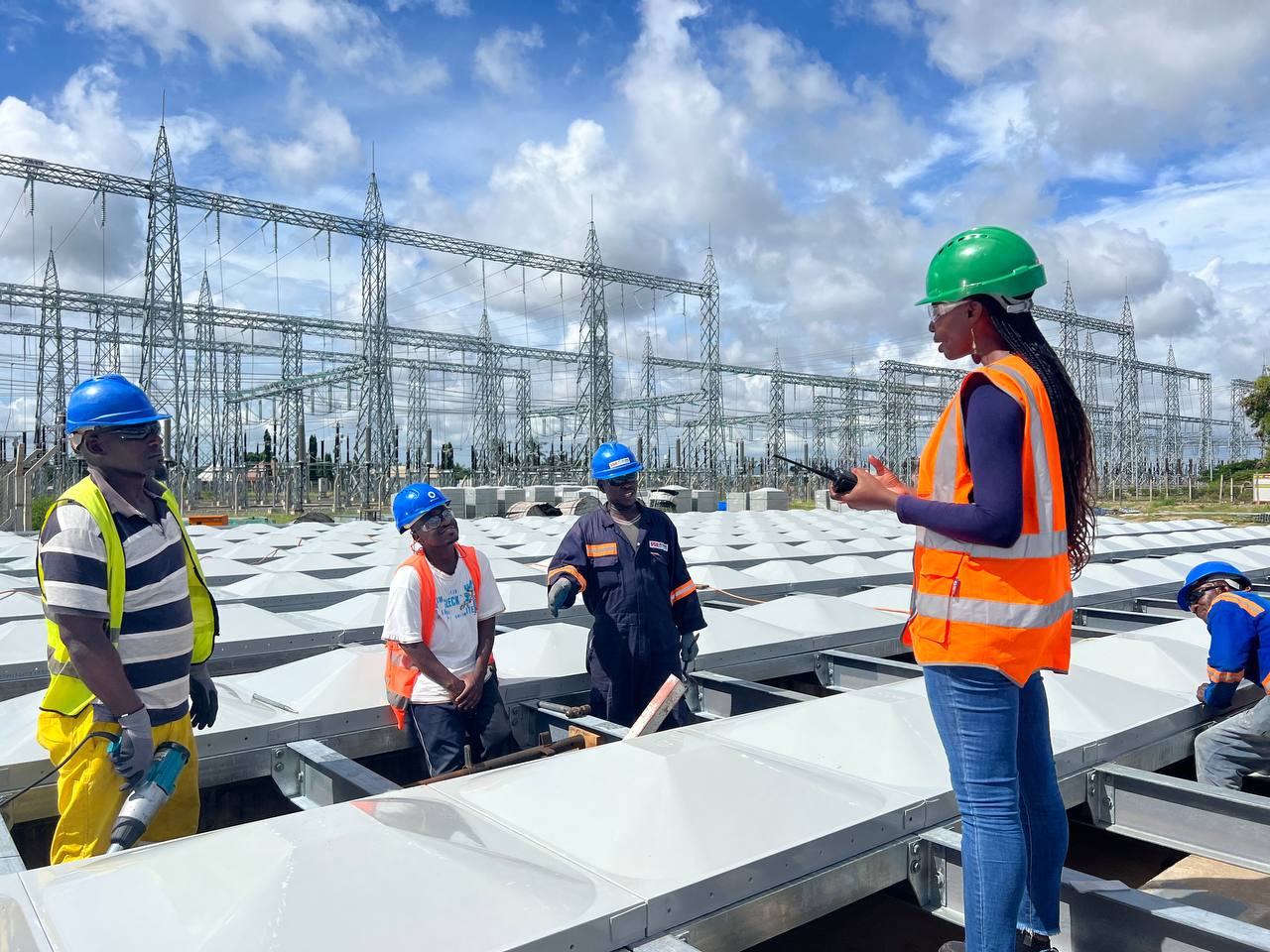
2. How do you ensure that contractors and subcontractors working on our projects are aligned with the company's Health and Safety policies and standards?
We take the health and safety of our employees and contractors very seriously. One of the ways we ensure that contractors and subcontractors working on our projects are aligned with our company's Health and Safety policies and standards is through a rigorous pre-qualification process. This process includes an evaluation of their policies and procedures. Only those who meet our standards are considered for the project. We do have principals and guidelines that all our subcontractors should follow:
1. First, we make sure that all contractors/ subcontractors are responsible for safeguarding their employees’ Health and Safety, by providing proper training and equipment for them to work safely
2. They must submit a risk assessment. Subcontractors should assess the workplace and identify potential hazards that could cause harm to employees. This assessment should include identifying hazards and mitigation measures for each task they will perform.
3. They should develop proper safety procedures. Subcontractors must develop written method statement for each job task that outline how to safely perform the task, and make sure that the team understands it well.
4. At CSI Energy Group, we conduct continuous training. We provide intensive induction which stipulates all safety requirements before commencement of work. Subcontractors also usually submits proof of training certificates for 1st Aider, HSE Representatives and other technical staff.
5. Provide adequate PPE. Contractors/Subcontractors should provide to their employees all the necessary PPE to protect against the hazards identified in the risk assessment.
6. Conduct regular safety meetings and auditing: We hold regular safety meetings to reinforce safe work practices and provide updates on any new hazards or procedures and address all the nonconformities.
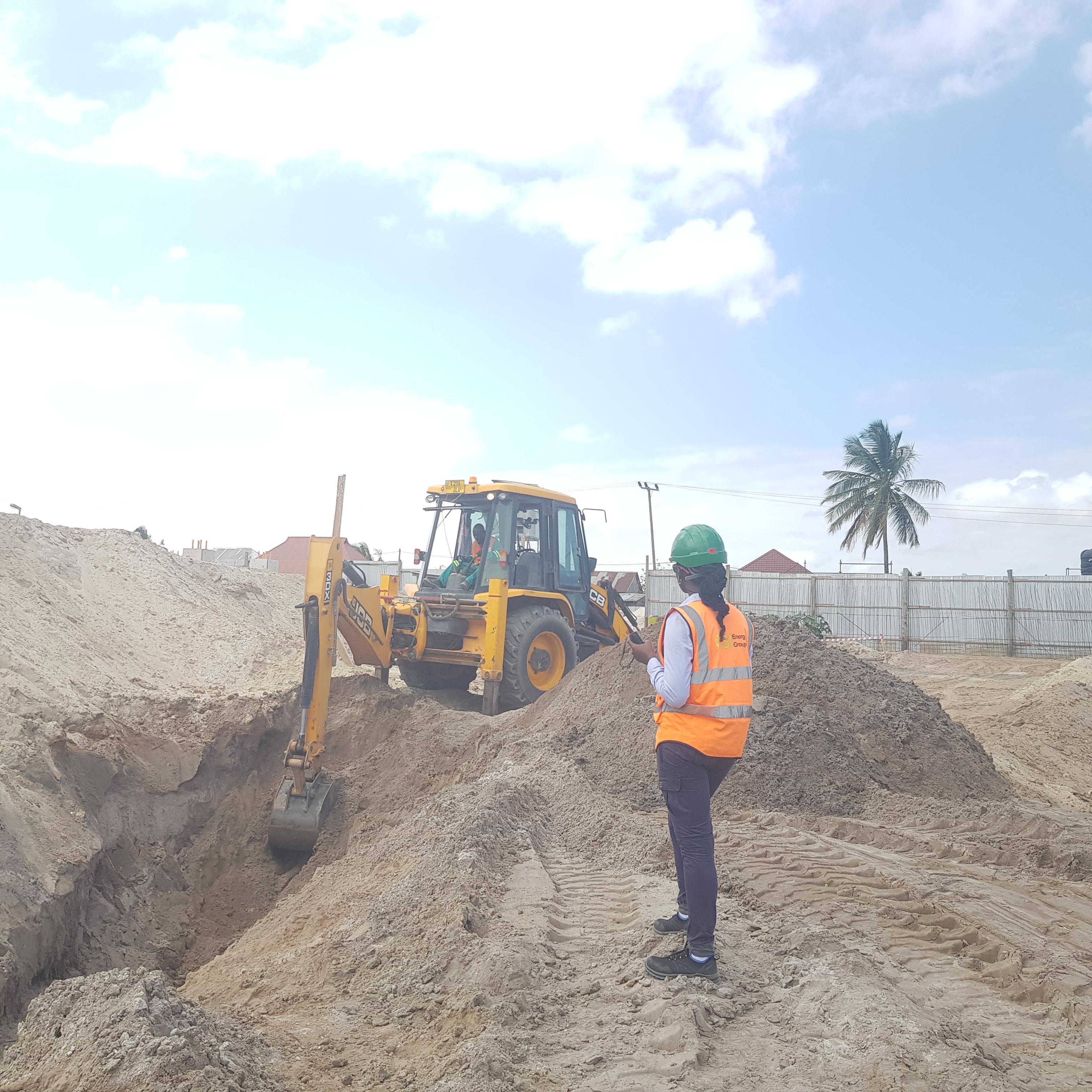
3. How do you ensure that Health and Safety considerations are maintained throughout the entire lifecycle of a project, from planning to decommission?
Maintaining Health and Safety considerations throughout the entire lifecycle of a project is essential for ensuring the well-being of our employees and contractors, protecting the environment, and promoting the sustainability of our communities. We have a comprehensive Health and Safety Management System that guides our approach to project planning, execution, and decommissioning.
During the planning phase, we conduct a thorough risk assessment to identify potential hazards and risks associated with the project. We also engage with stakeholders and local communities to ensure that their Health and Safety concerns are considered in the project design and planning.
Throughout the execution phase, we have a dedicated Health and Safety team that oversees project activities to ensure that they are being conducted in accordance with our Health and Safety policies and procedures. We also provide ongoing training and support to our employees and contractors to ensure that they understand their roles and responsibilities in maintaining a safe and healthy work environment.
In the decommissioning phase, we prioritize Health and Safety considerations to ensure that any potential hazards associated with the decommissioning activities are identified and addressed. This includes developing and implementing appropriate decontamination procedures, managing hazardous waste, and ensuring that all personnel involved in the decommissioning activities are trained and equipped with the appropriate personal protective equipment.
Additionally, we conduct regular Health and Safety audits and inspections throughout the project lifecycle to identify any areas for improvement and to ensure that our Health and Safety Management System is being effectively implemented.
It is a core value that underpins everything we do, and we are committed to continuously improving our Health and Safety performance to ensure that we operate in a safe and responsible manner.
4. How do you measure the effectiveness of the company’s Health and Safety management systems for projects, and what steps are taken to continuously improve these systems?
Overall, at CSI Energy Group, we implemented a Health and Safety management system, which is a continuous cycle of planning, implementing, measuring, and improving. We are taking these steps to ensure that our Health and Safety management systems remain effective and continuously improving. We ensure the following:
1. Occupational Safety and Health Administration (OSHA)/ NEMC Regulations are met. OSHA is a regulatory body that sets standards for workplace safety and NEMC for Environmental Matters, we ensure that all required compliances are met.
2. We provide Personal Protective Equipment (PPE) to all employees: Workers in our operations it is mandatory a to wear appropriate PPE such as hard hats, safety glasses, gloves, and steel-toed boots. This helps to protect workers from potential hazards.
3. Hazard Communication (HAZCOM): We communicate all the hazards to worker through risk assessment.
4. Site-Specific Safety and Emergency response Plan is in place and communicated: For us each site must have site-specific safety plans that outline the potential hazards and safety procedures specific to that site.
5. Training and Education: Employers are constantly trained and educated on potential hazards and safety procedures. This includes initial safety induction which is mandatory as well as ongoing safety training ie through Toolbox talk, safety programs etc.
6. Safety Inspections: Regular safety inspections are conducted to identify potential hazards and ensure that safety procedures are being followed.
7. HSE Policies are communicated and understood: HSE, Environment, Quality, Drugs and Alcohol Policies
8. Life Serving Rules and Permit to work – It is mandatory to know and understand Life serving rules, but also, we ensure work permit with specific certificates depending on what activities to be carried.
9. A monthly HSEQ report is compiled by external consultants and sent to the Management. We then have a monthly HSEQ review between the Management and all HSEQ staff to review the report together and more particularly the learnings, and proposed corrective and preventive action points, and make sure those are being effectively implemented.
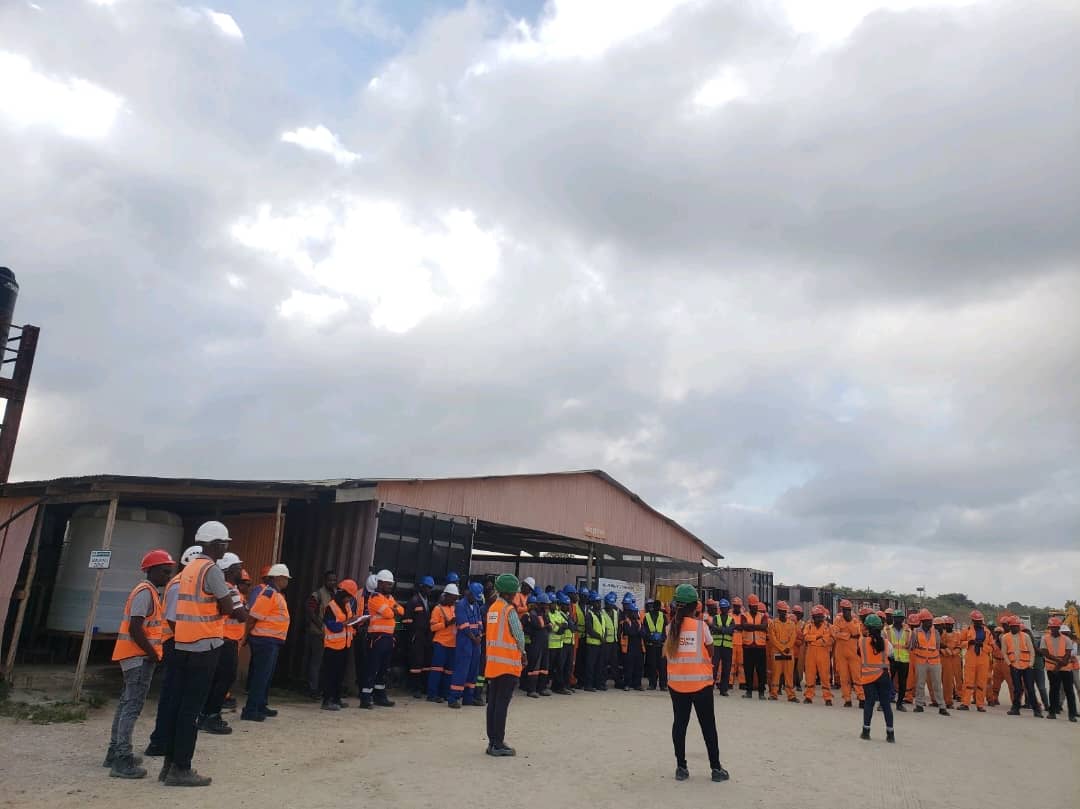
5. How do you work with local communities and stakeholders to ensure that their Health and Safety concerns are addressed during project development and execution?
Indeed, our operations have a direct and indirect impact on the local communities and other stakeholders. Constantly at CSI Energy Group, we address Health and Safety concerns during project development and execution, and we are guided by an Environmental and Social Management Plan.
1. We Identify stakeholders: all stakeholders who may be affected by the project, such as community members, workers, contractors, and government officials are identified before the commencement of the project.
2. We communicate in time with all stakeholders: Establish open communication channels with stakeholders to understand their concerns and expectations. Regularly engage with them through public meetings, surveys, and other means to keep them informed about the project's progress and any changes that may affect them.
3. Conduct Social impact assessments: Conduct impact assessments to identify potential Health and Safety risks associated with the project, and develop mitigation plans to reduce or eliminate those risks.
4. Involve stakeholders in decision-making: Involve stakeholders in decision-making processes that may affect their Health and Safety. Consult with them before making decisions and seek their input on how to address their concerns.
5. Provide training: Provide training to workers, contractors, and community members on Health and Safety issues related to the project. Ensure that all parties understand the risks and know how to take appropriate actions to prevent accidents or incidents.
6. Monitor and evaluate the project's Health and Safety performance regularly. Use feedback from stakeholders to improve the project's Health and Safety management systems and processes.
7. Providing Employment Opportunities: We provide employment opportunities to local communities and stakeholders, which not only helps to improve their economic status but also promotes a sense of ownership and responsibility for the project's success. This also enables us to build strong relationships with the communities and enhance their trust in our company.
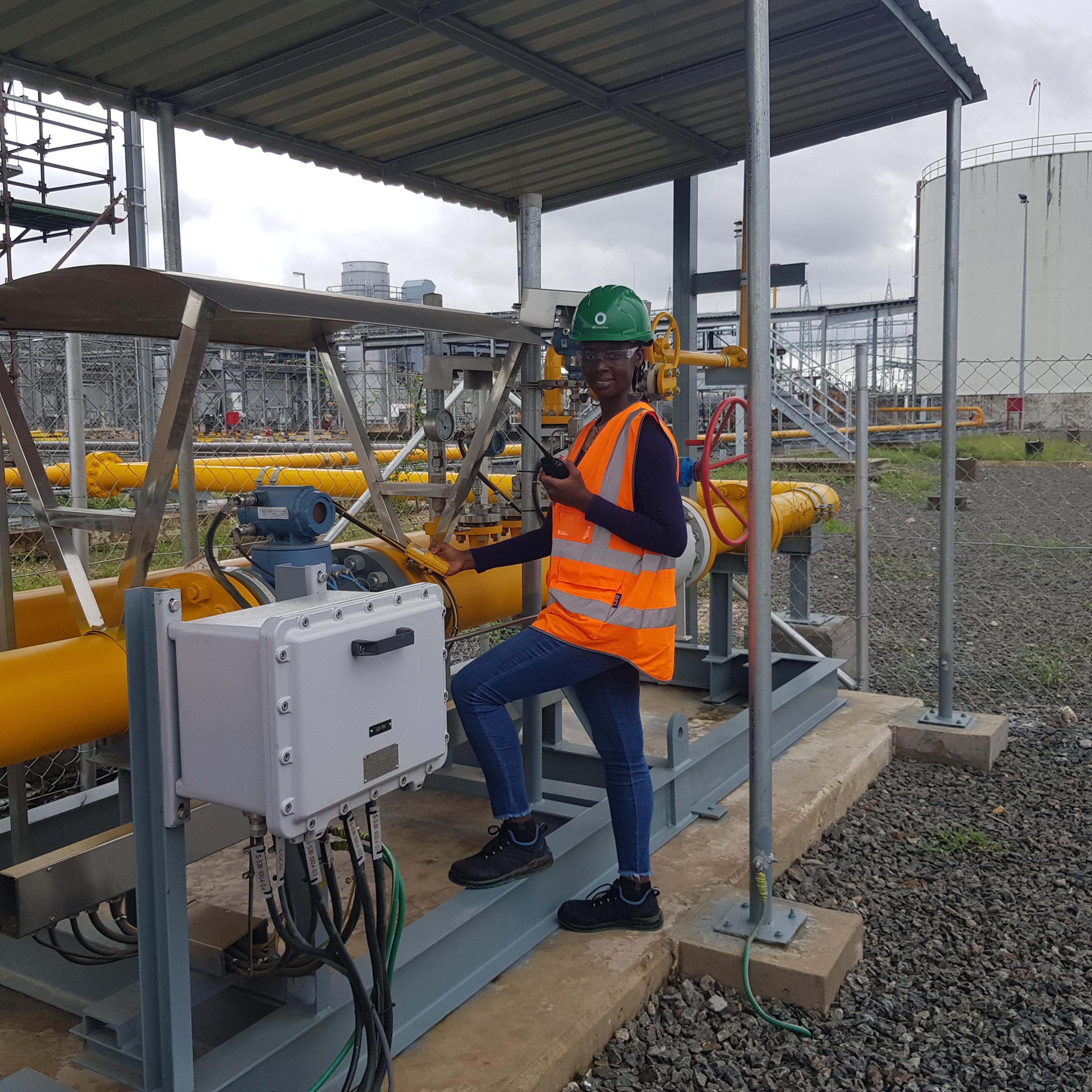